Start your project with Spark
Find a solution that's right for your business, on your terms.
Thank you! Your submission has been received!
Oops! Something went wrong while submitting the form.
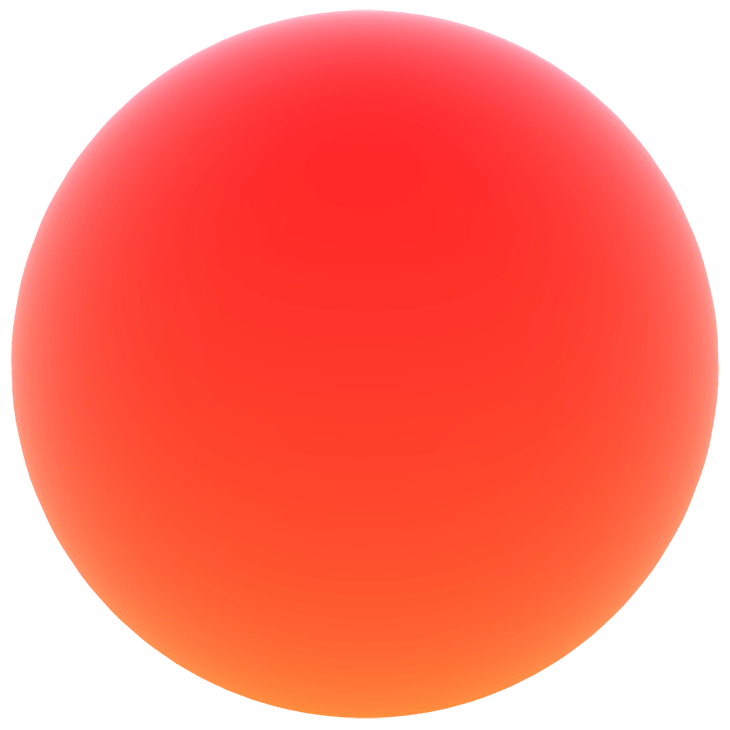
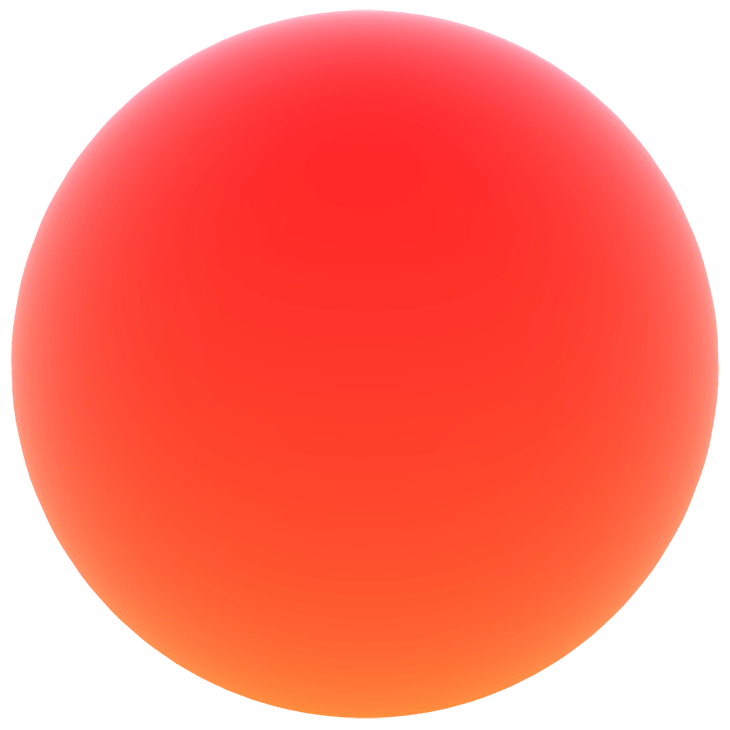
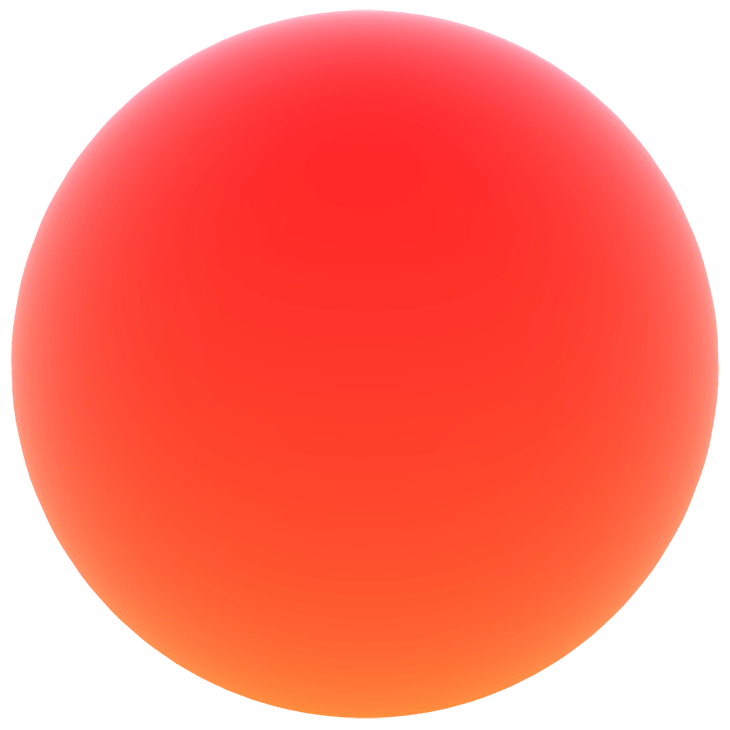
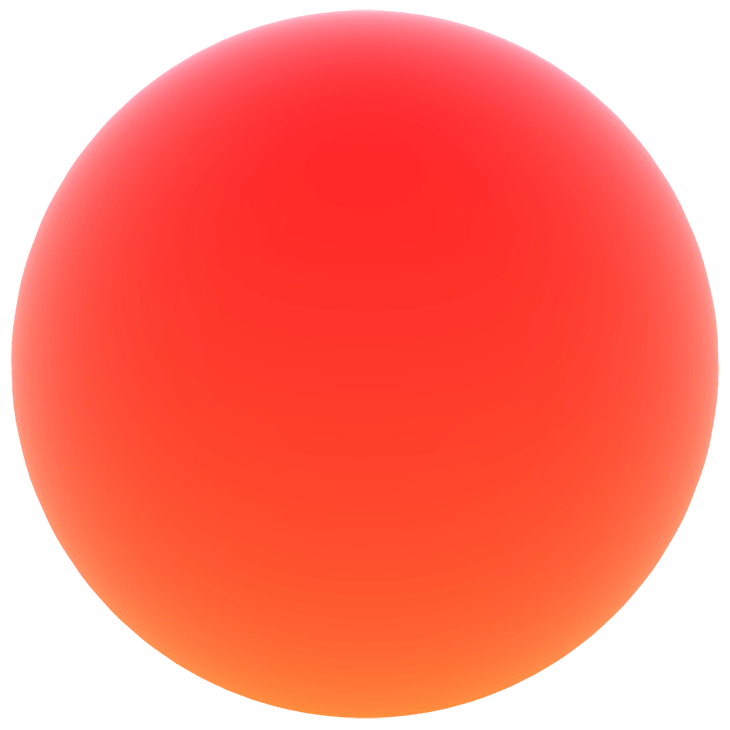
Manufacturing companies face complex challenges in a competitive landscape. To meet these enormous challenges, manufacturers have long invested in continuous improvement methodologies like lean manufacturing. Also, increasing numbers of manufacturers are adapting and investing in Industry 4.0 technologies to tame the complexity by increasing automation, adopting smart machines, and enhancing smart factories.
Technology upgrades and process improvements often go hand-in-hand. 67% of manufacturing organizations have sped up their digital transformation efforts since the beginning of the COVID-19 pandemic. Finding processes to improve can both help reduce expenditures and increase customer satisfaction. This post will cover four common areas manufacturers can optimize—whether via large changes or incremental improvements—that will offer outsized gains to the business.
[Inefficiencies and bottlenecks often remain hidden from view. Process mining tools shine a light on these problem areas. Learn more with the Process Mining Guide.]
To remain competitive, manufacturers must engage in continuous process improvement practices. Customer satisfaction relies on timely product deliveries, so boosting efficiency must remain top-of-mind. One solution comes in the form of process mining tools. Process mining tools track real-world processes and automatically map them to business process diagrams so you can see how work occurs on the shop floor. While you may know some of your current bottlenecks, process mining almost always uncovers new opportunities for improvement. This can be particularly helpful in finding “hidden factories” within the organization that may be slowing down the production process. For example, you might uncover that certain teams batch upload spreadsheets instead of using existing software solutions. This shows a perfect opportunity to modify your processes to accommodate the team’s workflow and introduce standardization to the group.
With the advent of the industrial internet of things (IIoT) devices, manufacturers have had unprecedented opportunities to improve connected equipment performance. Equipment downtime contributes significantly to manufacturing costs, both due to work stoppages and unplanned maintenance expenses. Organizations must work to maximize equipment effectiveness (OEE)—which measures current equipment effectiveness against maximal capacity—so the production line runs at peak effectiveness. IIoT technology can help improve OEE by allowing you to automate continuous maintenance checks on equipment, note flagging performance indicators, then assign technicians to perform maintenance before it becomes a problem. This predictive maintenance outperforms traditional scheduled maintenance and can dramatically reduce costly downtime. In fact, according to Deloitte, predictive maintenance can decrease machine breakdowns by 70%.
Additionally, with increased emphasis on sustainability and environmental issues, organizations must measure their environmental footprint and reduce different types of waste. Monitoring resource consumption while also reducing scrap and rework can curtail emissions and pollution. And with governments passing new regulations around carbon pollution and many companies demanding environmental, social, and governance (ESG) data as part of their RFP process, it's critical for businesses to minimize their negative effects on the environment. Process mining can play an important role here as well, allowing you to discover processes that produce additional material waste so you can create an action plan to mitigate this issue.
Manufacturing operations have already seen the benefits of automation. However, there are still plenty of opportunities for ongoing improvement, particularly to business processes and workflows. Not only will this reduce labor costs and improve product delivery time, but by automating repeatable processes, manufacturers can reduce human error that leads to scrap and rework.
The trick is to find any systematic process with repeatable steps that can be offloaded to automated floor equipment or software automation tools. For example, automation tools—including artificial intelligence and machine learning—can be used to notify team members when a potential problem looms on the production floor so they can fix it before the issue materializes. Again, process mining tools can help by demonstrating repetitive manual work streams ripe for automation. Once process mining uncovers these areas, you can leverage workflow-driven design and automation tools to further improve turnaround times, lower labor costs, and reduce redundant manual work.
Another area ripe for improvements is supply chain management. According to KPMG and Forrester, 80% of manufacturing organizations stated that developing a more responsive supply chain was a top digital transformation priority. Gaining increased visibility into both your own systems and across your vendor ecosystem gives you better information to optimize inventory levels, thus reducing inventory waste while also minimizing shortages.
It starts with connecting systems. Enterprise resource planning (ERP) systems, inventory and warehouse management systems, and transportation systems should all be unified to allow greater transparency on where products and parts are. Connecting internal systems to those from third-parties can be beneficial as well. For example, gaining data from online orders and point-of-sale systems for either your customer-facing wings or the companies you supply can generate real-time demand signals that allow planning teams to take a data-driven, systematic approach to better predicting needed supplies. Manufacturers should look for a way to bring this information into a unified system that allows them to monitor key performance indicators across their supply chain to further develop resilience.
[Supply chain management requires adaptability. Take an in-depth look at building resilience with the eBook Bringing Clarity to Supply Chain Chaos.]
Last, but certainly not least, your organization's ability to quickly adapt to change makes a major difference in controlling manufacturing costs as well as improving customer satisfaction.
There are two key factors in operational agility. The first is the ability to quickly adapt to market changes. Examples here include adapting supplies to meet quickly to shifting market demand signals or from quickly rolling out new products or services.
Perhaps even more important is the ability to implement process improvements in a short period of time. Whether they're incremental improvements or sweeping changes, process optimization efforts should have a fast time-to-value. One of the best ways to do this is via a unified process automation platform with low-code capabilities.
Low-code offers the ability to improve business processes by delivering applications up to 10 times faster than traditional development. If current processes have room for improvement, low-code can help you create new applications, extend the functionality from existing applications, or orchestrate changes between existing solutions to help with continuous process improvement.
Let's take an example from earlier—predictive maintenance. Your development team can use a process workflow diagram to map the ideal steps for running predictive maintenance. They can have the system run continuous maintenance checks that trigger alerts when equipment performance could become an issue. From there, they can use automation tools like business logic and robotic process automation to schedule the closest technician to perform maintenance at the appropriate time. If you find further process improvements in this scenario, you can then modify and tweak the process to make it even more efficient.
Process automation platforms can play a major role in manufacturing process improvements. A great platform will connect three main areas—workflow, automation tools, and process mining. Of particular import here is process mining. Process mining tools allow you to automatically view how processes run in the real world so you can find hidden bottlenecks, then track performance for continuous improvement. While you likely know a lot of your inefficient processes, seeing how processes are done in the real world nearly always uncovers hidden issues that keep organizations from achieving more positive outcomes. Once you find these issues, you can develop an action plan to implement changes using the other tools in the platform (and then use process mining to track the impact). The result? Lower costs to manufacturers, easier processes leading to boost in morale, and an overall increase in performance for the company.
To find out more about how to find process improvement opportunities, get the Process Mining Guide.
Written by Gary Cassell, Industry Lead, Manufacturing and Automotive, Appian
Appian Partner: View Manufacturing Solutions