Start your project with Spark
Find a solution that's right for your business, on your terms.
Thank you! Your submission has been received!
Oops! Something went wrong while submitting the form.
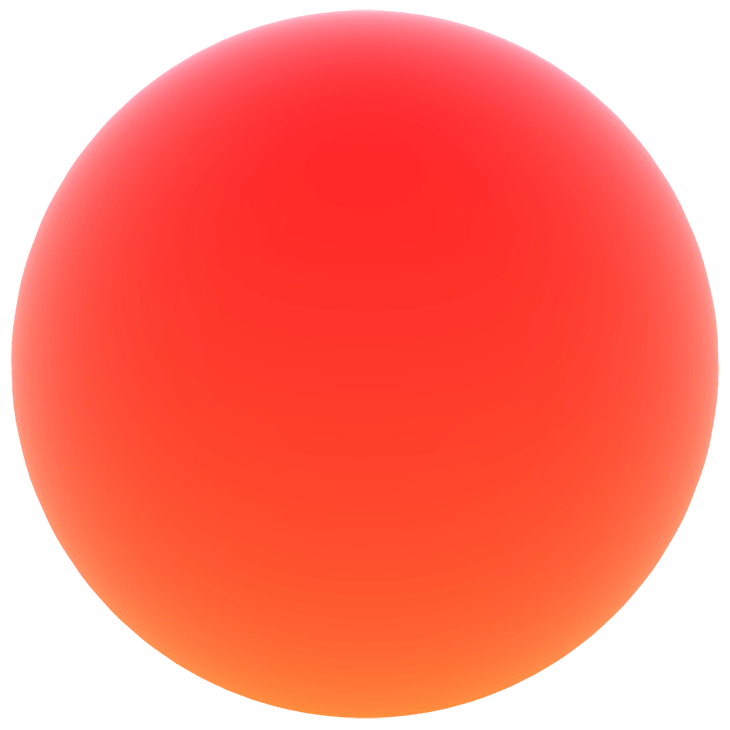
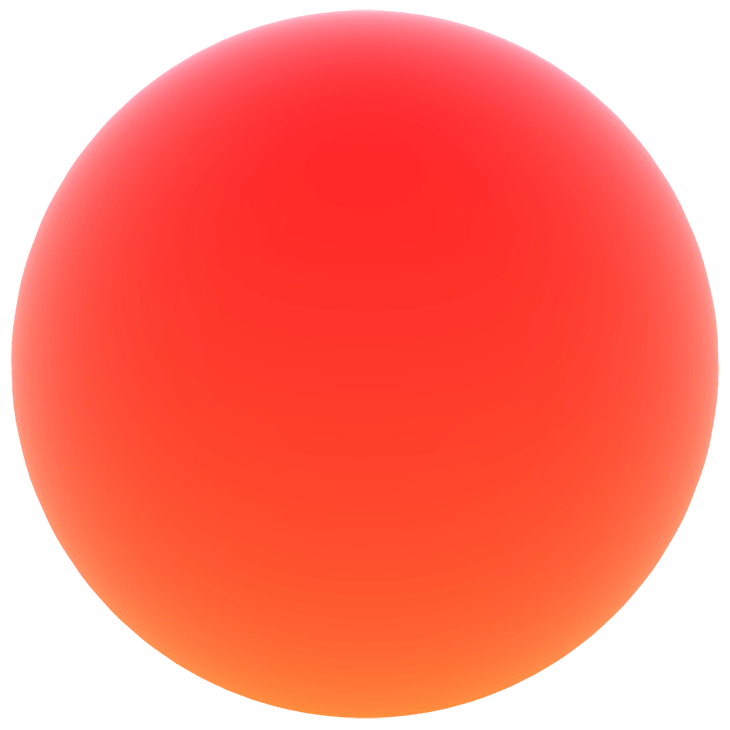
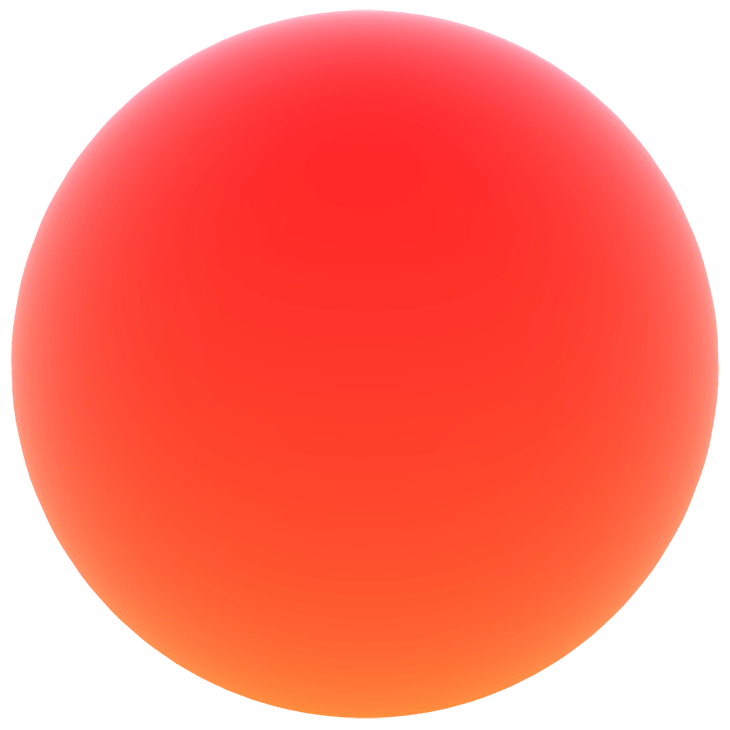
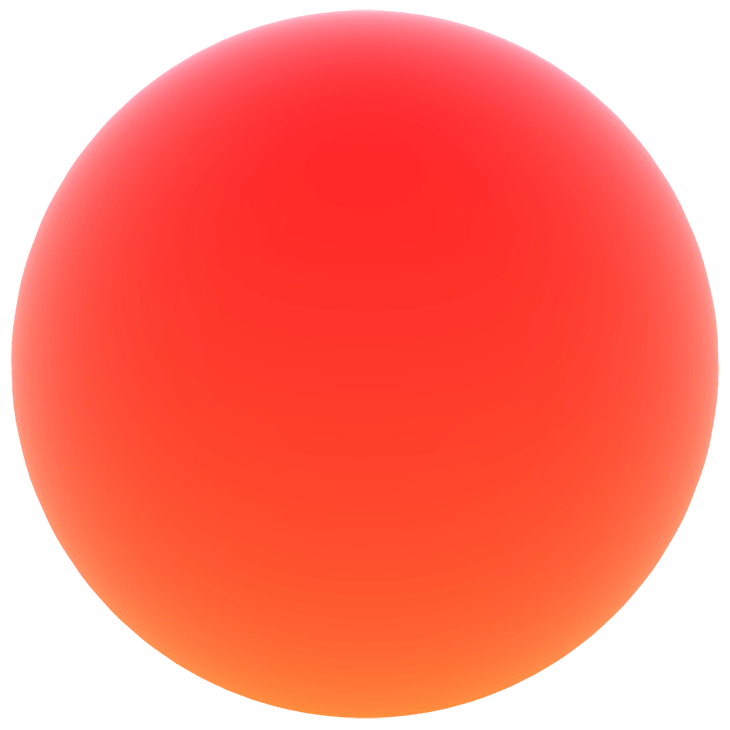
Done right, data alignment will slingshot your manufacturing business to the moon. Done wrong, it will keep you up at night.
Supply chains are disrupted, eco-compliance is changing, and onshore manufacturing is back en vogue, along with labor shortages. There has never been a better time than now for smart manufacturing.
A smart manufacturer uses data to guide their decisions. The better the data is organized and understood, the better and faster business decisions are made.
You can use tech to take something complex (data), simplify it for easier readability (analytics), and apply the findings to guide your actions.
Source: 2023 Deloitte Manufacturing Outlook Survey
Most manufacturers are on their way toward smart manufacturing. Of these, however, the majority is struggling to see value. According to a 2021 WEF study, 61% of manufacturers fail to have scaled data-driven production beyond a single product.
For those that have, the outcomes according to McKinsey are:
There are three areas to focus on to see results like the ones above.
Pro tip:
A key reason for data-alignment failure is misalignment of people. Your company culture will change, as you embark on this journey. The intent needs to be clearly communicated by upper management to your people, at every level. And you need to update your people on the results, as they come.
You can’t run a factory in the cloud.
This doesn’t mean that you don’t need the cloud - you do. It means the IT infrastructure on your factory floor should be robust enough to support the data needs of OT.
The thousands of endpoints on machines, robotics, devices, and monitors generate data and require data to operate.
Cloud computing calls for moving data to the cloud for processing, then returning it to your location to feed into the equipment that requires it. This is a highly latent, slow process, which additionally suffers from the insecurity of the open internet.
The alternative is to apply the edge computing paradigm. Edge computing refers to deploying IT infrastructure including AI/ML and running data analysis right where your data lives - on your factory floor.
Edge is not an alternative but a complement to the cloud. Instead of collecting data off-site, sending it to the cloud to process, then acting on it, you are:
As a result, your factory is running at optimal capacity and your supply chain is up-to-speed.
Here are a few reasons to opt for edge computing:
Let’s take a look at some use cases where edge computing makes all the difference.
Predicting when a machine will fail and servicing it prior to failure has been a bit of a holy grail for manufacturers. Unfortunately, few have been able to achieve it.
Some problems got in the way. Such as not enough data points collected and analyzed to provide a reasonable base for prediction and difficulty with getting data from equipment into IT systems.
Edge computing can change this. Provided your data strategy calls for the collection of enough data points, you can build predictive machine learning models running right at the edge, at your factory. These models can with a high degree of likelihood predict servicing needs for the equipment in question.
Another holy grail is adjusting manufacturing in real-time, based on the state of equipment and manufacturing process. Such a process becomes possible through the collection of enormous data volumes and further analysis with AI/ML.
Again, how such a process is implemented is up to you and should be a part of your data strategy.
Sensor-equipped employee badges or hardhats can send location data to be processed. Employees, contractors and visitors can be alerted and stopped when they happen to be in a dangerous area. In the case of an emergency evacuation (fire or other industrial accident), data on all employee locations can be accessed by management through mobile web interfaces.
Your data strategy defines what data you collect and how you use it to achieve business goals. It also addresses the people and processes that will support your data practices.
In manufacturing, data strategy is first and foremost about the convergence of operational technology (OT) and information technology (IT). OT is responsible for interacting with the physical world - control systems, logic controllers, etc. IT is responsible for data systems and solving end-user problems.
How to define a data strategy:
1. Define your business goals
Define or study and update your business strategy and objectives. Focus on long-term and short-term goals.
At this stage, you should define your data team and involve them in the ideation process.
2. Identify your use cases, data sources, and insights you are after
Your data is only as good as the insights it gives you. At this point, you are defining what outcome you want to generate from your data. This concerns factory outcomes - edge use cases, as well as higher-level operational monitoring outcomes.
Identify the entire variety of data that you have access to. Your factory equipment likely generates data at every step of its operation. You may have to work with the vendor to ensure that you are able to collect the data you are after.
Ask yourself which data can generate the insights that will help you to achieve your goals. This is the data you want to focus on.
3. Review your current infrastructure
You cannot pour new wine into old skins. You cannot store, process and use data on legacy infrastructure.
Are you running in the cloud? When did you implement your ERP? How aligned is it with your goals? What problems do you users report with it? What manufacturing equipment are you using on the factory floor? What data do they need to operate?
You also might conclude that you need to revamp your infrastructure or update parts of it.
Sometimes a look from the outside can make all the difference in the world. We specialize in infrastructure review, do reach out.
4. Structure your data
Establish naming and value conventions. Decide on structured or unstructured. Establish metadata access and referencing guidelines for data sets.
5. Document your data processing and workflows
Define who the target consumer for the data is. Is it someone on your data team or is it a device on your manufacturing floor?
A smart manufacturer’s data-driven production is powered by the data it generates. Being able to act on data in real time on the factory floor is a game-changer for any manufacturer.
Your operational technology - endpoint devices, robotics and machines send and receive massive amounts of data. Uninterrupted automated production relies on data flow. This means deploying a robust on-site network, in the edge computing paradigm.
6. Define processing, networking and storage architecture
If you choose to go the edge computing route, running the calculations in real-time on the factory floor will have a profound impact on your operations. You can expect increased throughput, reduced waste, increased predictability and reduced downtime.
At this stage you also need to define your cloud policies for data storage and accessibility.
7. Establish a continuous improvement of data processes pipeline
Data process pipeline is not a thing set in stone. You will need to apply the same continuous improvement practices to it, as you do in your production. (more below)
8. Data governance and insights propagation
What data governance is not: gatekeeping.
What data governance is: a single framework to enable ease of data use and access for all data users.
Present to the wider team on the outcomes of your data strategy. Insights, improvements and changes to the business. Don't limit yourself to the data team - inform everyone.
It can be easy to think “they work the factory floor and they see the changes daily”. Don’t. Be vocal about your goals and how you are achieving them.
Lots to remember here. Download the strategy as a checklist for reference.Expand
I decided to bring this section out on its own because of how important it is not to stagnate in thinking you have got it solved with your data strategy.
Immediately upon kicking your data-aligned production into gear you will come upon bottlenecks. This is fine. You can be ready with continuous data flow improvement.
Use a framework to make sure continuous improvement takes root in your data team. You may have heard of or used Goldratt’s Theory of Constraints. You can also apply it for your data
The theory states that constraints limit the output of any system.
The constraints can exist within your manufacturing facility or business processes. They also may exist outside your org - in the supply chain or the market.
Here is the continuous improvement process as seen through the lens of TOC:
....
Here is an example of how a client applied TOC to solve a supply chain problem.
Background:
A sheet metal fabrication company in the process of data-alignment. Edge computing deployed in part of production facilities, integrated with cloud data storage and ERP.
Problem:
The system has started falling behind in producing orders composed of aluminum.
Identify:
The data team had to identify the constraint. What is going wrong in the current system? After some digging, they realized that the constraint is GTAW electrode wire. They were running out on a regular basis. This is the wire used in welding aluminum at the factory. The robotic welders have nothing to weld with. Human operators scramble to refill the supply but time is still lost.
Exploit:
Adjusting the available resources to fix the bottleneck in this case means finding a data solution to pre-order electrodes before they run out. The issue with this is that such a system was set in place but, apparently, not achieving its intended function. It turned out that the system monitored the supply of all electrode wire, not by electrode wire type.
Subordinate:
Data team rewrote the data flow to monitor for every type of electrode wire quantity and pre-order two weeks before the stock is set to run out.
Elevate:
The data team ensured a stable stock of electrode by wire type not only for GTAW electrodes, as well as all the other electrode types used at the factory. In the next month, the factory saw throughput grow by 4% over intended targets across the board. What was once a constraint in a single area of production, became an asset for the entirety of production.
Repeat:
The data team are on the look out for the next limiting factor.
....
The right mix of technology adoption can strengthen the manufacturing core while pushing the edges to improve efficiency.
We live in an interesting time. SMBs not only can use technology and processes previously only available to enterprises, but can beat enterprises in terms of speed and efficiency.
For a manufacturer, this can mean establishing a low-code/no-code practice to speed up their time-to-product. Instead of building dashboards and data silos from scratch, in 2023 you can use low-code tools such as Appian (our trusted partner) to build products fast.
It’s a great tool in the continuous data flow toolbox. You won’t have to wait weeks and months for IT to make changes to the application, the edits can be as fast as a few hours or a day.
People and technology are often at odds with each other. The future of manufacturing is with technology that supports the human. Already now you can arm your workforce with the exact tools they need to be as innovative and effective as possible. This augmented workforce won't need to adapt to machines but instead will be enabled by technology to be at their very best.
Let us know if you need any elaboration on the above, want to bounce some ideas off of us or if we left anything out.